by: Anastasios Dimas, Regional Digital Delivery Lead, Middle East & Africa and Attila Vidra, Digital Lead, Land Development, Middle East & Africa Atkins, a member of the SNC-Lavalin Group
The Middle East construction industry is seeing strong growth, particularly in Saudi Arabia and the UAE where megaprojects are increasing opportunities for innovation and collaboration. With the regional market valued at US$ 1.8 billion in 2022, and expected to grow at a significant rate of 6.3% between 2023 and 2028 , investment in construction technology has also doubled in the past decade , as the industry recognises the power of innovation to transform every element of the construction process.
While combining smart technologies and digital solutions to make operations more efficient, safe and cost-effective is a focus for the industry, the move towards more sustainable operations is also a key objective. The wider adoption of new technologies, such as Augmented Reality (AR), robots and 3D printers, is accelerating the transition towards net zero emissions, helping projects finish quicker, with less material and energy waste. With the UAE hosting COP28 later this year, the region is positioning itself as firmly committed to decarbonisation efforts and exploring net zero strategies across all operations.
Adoption of digital models to drive innovation
Data is the thread that connects traditional practices with future solutions and has the power to transform outcomes. While the construction sector has been slow in adopting digital driven solutions compared to other industries, advanced methods of data capture are becoming increasingly important to push its evolution.
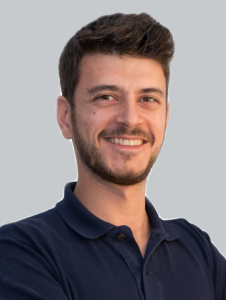
Take onsite operations as an example. We are already seeing innovative uses of current technologies such as smart sensors and handheld 3D laser scanners to offer safer and more efficient data collection. Quickly capturing high-quality footage, these provide data-driven insights to help influence decision-making, while minimising onsite risks. The application of machine learning to analyse this data is also evolving, enabling optimised approaches to site operations, design, health and safety, risks and much more, building greater efficiencies across projects.
Digital technologies such as robotics and drones are already playing a key role in enhancing data collection and machine learning processes. In the Middle East, robots can help conduct construction site reviews safely – especially with harsh summer climates and megaprojects spread across remote areas. For example, Atkins used Boston Dynamic’s Spot robot to conduct routine monitoring and surveys in its nuclear operations for the US Department of Energy, driving greater efficiencies, minimising risks to humans and supporting progress towards net zero goals. This offers learnings to replicate in the built environment. In a similar way, drones are providing faster and safer data collection, cost savings and improved communication.
Countries across the Middle East are also recognising the potential of these technologies, with efforts made to update regulations and policies to support their use. Earlier this year the UAE introduced new laws to govern the design, building and use of drone near airports in Dubai, aiming to enhance the safety and security standards. As more countries follow suit and update laws that enable their wider adoption, it is expected their use will become more common in industries such as construction and this will also lead to an upskilling of the workforce to help them better understand these technologies.
Harnessing the power of data for digital design
As these technologies provide more robust data sets, the first step towards maximising the value of this is through digital design. Setting a benchmark for the region in the transition from 2D to 3D design, Atkins worked as the lead designer for Qetaifan Island North in Qatar, pioneering digital technology to create comprehensive 3D modelling. While this is now becoming common practice, the models could also be viewed in a centralised platform, utilising Virtual Reality (VR) technology to drive collaboration from stakeholders around the world.
Today, more projects are adopting these design methods, exploring extended reality to enhance complex data visualisation. In particular, VR is enabling a fully digital experience where project stakeholders can view 3D project models – and even walk through buildings – through a headset from anywhere in the world. This is particularly beneficial to drive collaboration, build workflow efficiencies and inspire greener operations, but also provides a virtual training tool in a safe learning environment. Mixed Reality (MR) and Augmented Reality (AR) are also proving to be useful onsite tools. Keeping a connection with the real world, MR enables site visitors to interact with digital and physical objects in tandem, utilising data to add holographic information to offer better interpretation of the project and review issues faster. Meanwhile, AR provides the same digital graphics through a mobile device.
Each of these have a part to play in the Middle East construction industry’s future, enhancing collaboration, productivity and helping towards net zero targets. However, the vast potential must be balanced with the need to protect sensitive data, and this is where enhanced processes, education and industry-wide regulations come into play.
Transforming the physical world
While these technologies are reshaping the digital landscape, modular construction and 3D printing will revolutionise the physical. Examples of prefabrication and modular construction have been seen across the Middle East, mainly in some residential sites by using controlled environments for production with less waste and better quality to accelerate efficiencies and project delivery timescales. However, technological advancements will see 3D printing scale up this activity, providing benefits including reduced supply costs, decreased build times and simplified planning, along with the creation of greener process and sustainable buildings.
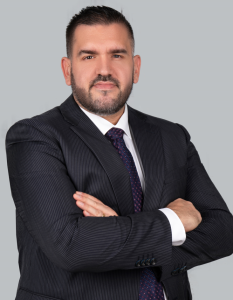
Atkins, a member of the SNC-Lavalin Group
Smaller-scale applications are already present, with the first 3D-printed house in Beckum, Germany, and a 3D-printed villa in Riyadh, Saudi Arabia, for example. Dubai is also home to the world’s first 3D-printed commercial building , which produced 60% less construction waste when compared to traditional methods of building. We predict it will be adopted on a much larger scale over the next decade, exploring new solutions to current challenges of high costs and scalability. The advantages are hard to ignore, and as more governments recognise its prominence – for example the Dubai Government’s ‘Dubai 3D Printing Strategy’ has pledged that 25% of new constructions will use this technology by 2030 – it’s only a matter of time before it moves from aspirational to common practice across construction.
Embracing the shift
It’s clear that technology is transforming almost every aspect of the construction process. We can see individual and small-scale implementation of tools, however, to help accelerate innovation and bring forward solutions to enable wider adoption across the Middle East’s built environment, collaboration is crucial.
Together, all stakeholders must create a healthy ecosystem that promotes investment in new solutions and training to help better connect people with new technology. By combining digital knowledge and learnings and enhancing processes and regulatory frameworks, the construction industry can unlock long-term benefits to operate more efficiently, safely and sustainably.